May 04, 2025
Supply Chain Reset 2025
About Author: Mr Bala A Kumar ( Bala) is a Director at Jayam SCM Consultants. Comes in with over 40 years of experience across industries across geography having been at many Leadership levels. Bala can be contacted at bala@jayamscmconsultants.com
Supply Chain Reset 2025
Is Your Strategy Ready for Tariffs & Geopolitics?
Tariffs, Trade Blocs, and India’s Emerging Manufacturing Opportunity**
The pandemic taught us about supply chain resilience. Now, a new wave of disruption – tariff wars and geopolitical decoupling – demands a fundamental reconfiguration. This isn't just about managing risk; it's about strategically redesigning for a new reality.
Executives are facing headwinds like cost inflation (~38%), economic uncertainty (~36%), and significant tariff exposure, particularly impacting sectors like electronics and semiconductors reliant on global components.
The emergence of manufacturing hubs in India, Vietnam, and Mexico offers a pivotal opportunity for automotive and automation industries. The 2025 supply chain playbook requires proactively mapping tariff exposures, strategically diversifying sourcing, and embedding digital visibility. Leadership in change management and a focus on tech-enabled shopfloors are also paramount.
The window for decisive action is narrow. Let's discuss how to move beyond disruption management and build truly resilient, future-proof supply chains.
From Pandemic Disruptions to Tariff Realignments
The COVID-19 pandemic taught us hard lessons in resilience, visibility, and agility. But the next wave of disruption — tariff wars and geopolitical decoupling — poses a different kind of challenge:
Pandemic Disruption (2020–2022) | Tariff & Trade Disruption (2025) |
---|---|
Health crisis and supply stoppages | Policy-driven tariffs and trade restrictions |
Demand collapse and rapid rebound | Prolonged uncertainty and cost volatility |
Focus on continuity and risk management | Need for structural reconfiguration and relocation |
Global “just-in-time” challenged | Rise of “friend-shoring” and “near-shoring” |
New Headwinds for Supply Chain Leaders
Recent global surveys indicate that executives are grappling with multiple pressures:
- Cost inflation (~38%)
- Economic uncertainty (~36%)
- Workforce shortages (~35%)
- Tariff exposure (cross-sector impact)
Industries Most Impacted by Tariffs
Industry | Why Impacted | Key Risk Elements |
---|---|---|
Electronics & Semiconductors | China is core to PCB, chips, components | Component cost hikes, supply shortages |
Automotive (Vehicles & Components) | Mexico & Canada integral to NAFTA/USMCA auto supply chains; China key for EV parts | Cross-border cost hikes, disrupted assembly timelines |
Industrial Automation & Machinery | Automation parts (motors, sensors, robotics) heavy China exposure | Price hikes, long lead times, production delays |
Pharmaceuticals & APIs | China key in APIs (Active Pharmaceutical Ingredients), India next largest | API shortages, drug cost spikes |
Steel, Aluminum & Metals | Tariffs on Canada, China directly impact input costs for manufacturing, infra | Raw material cost surge |
Textiles & Apparel | China/Mexico big exporters of fabric & garments | Retail price hikes, sourcing shifts |
Solar & Renewable Energy | China dominates solar panels, batteries | Project cost escalations, slowdown in installations |
Consumer Goods & Furniture | China is backbone of global consumer goods exports | Cost inflation in retail, slower inventory flows |
Chemicals & Specialty Chemicals | China key in rare earths & intermediates | Input shortages, increased costs for manufacturing |
Tariff War Impact
The ongoing tariff wars are not merely a disruption; they are a catalyst for a fundamental global reconfiguration. The shift from a 'centralize–outsource–scale' model to more multi-local, regionalized sourcing, evidenced by the emergence of significant trade blocs (US–India, US–Mexico, China–ASEAN, etc.), presents both challenges and opportunities. While operational risks like procurement delays and price hikes on critical components are undeniable, proactive leaders will view this as an impetus to strategically reimagine their supply networks.
Practical Implications - Focus on Proactive Measures:
"For automobile manufacturing and automation, where supply chains are often heavily Asia-centric, the exposure to tariff cost hikes is significant. However, this necessitates decisive and forward-thinking action. Manufacturers are now presented with the opportunity to:
- Strategically Redesign Supply Networks: Actively explore and establish alternative sourcing in regions like India and Vietnam. India, in particular, has a window to capitalize on this shift, but swift action is paramount to gain an edge over competitors like Vietnam.
- Implement Smart Inventory Strategies: While stockpiling carries risks, intelligent inventory management, informed by predictive analytics, can buffer against immediate tariff impacts without tying up excessive capital.
- Optimize Product Roadmaps: Strategically align product launches and lifecycle management with the evolving trade landscape
India’s Moment: An Emerging Manufacturing Powerhouse
- According to World Data Lab, India is set to add 47 million consumers to the global middle class by 2025 — surpassing both China and the rest of Asia.
This demographic dividend, coupled with government incentives and growing manufacturing capabilities, positions India as a strong contender in the global realignment
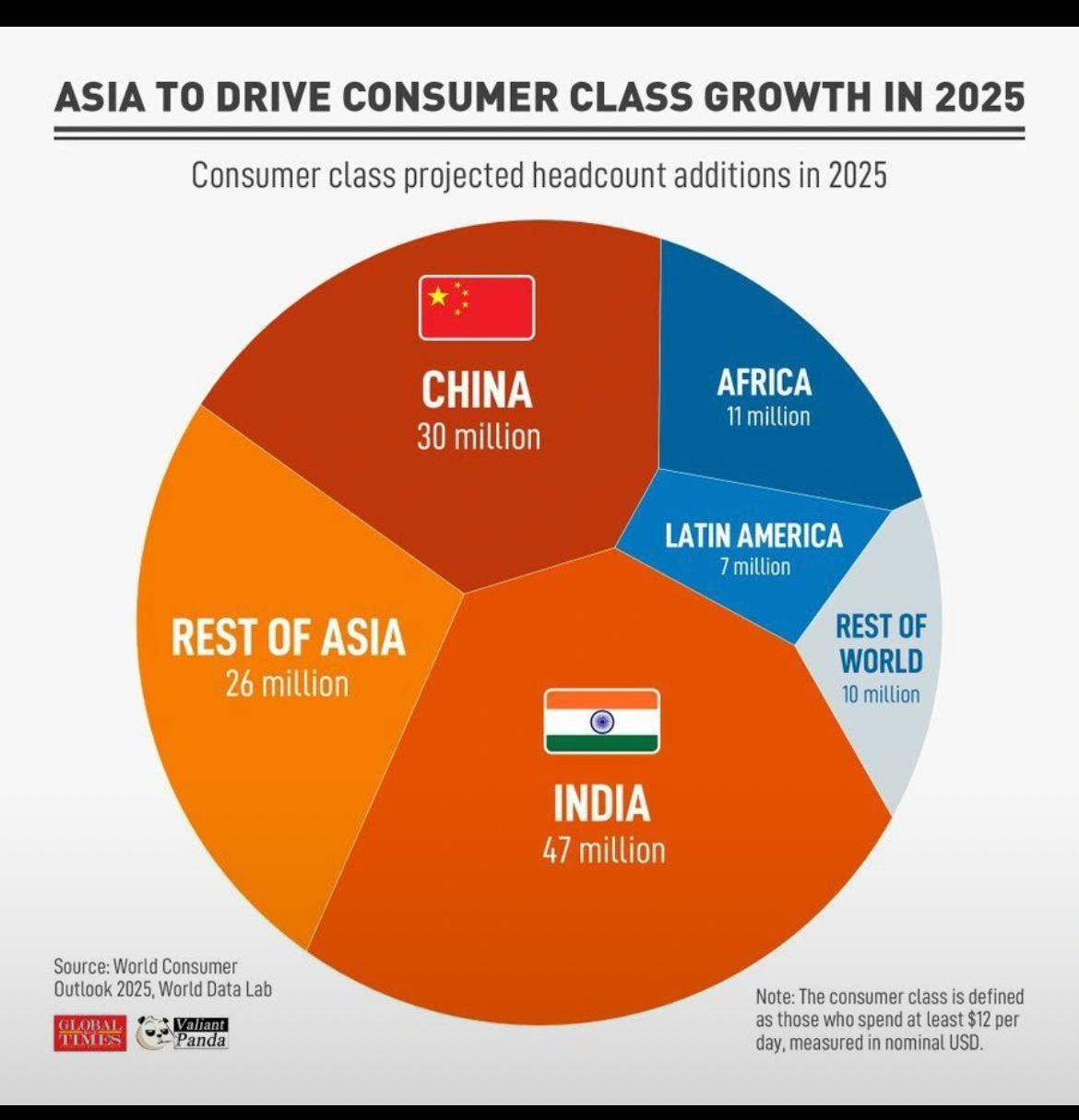
Sectors where India can lead:
Sector | India's Strength |
---|---|
Pharmaceuticals | Mature export infrastructure |
Auto Components | Robust supply chain ecosystem |
Electronics | PLI schemes; expanding FDI |
Specialty Chemicals | Cost advantage & scale |
Textiles & Apparel | Shifting US/EU demand |
Renewable Energy | Solar manufacturing & steel focus |
With Production Linked Incentives (PLI), policy support, and large-scale infrastructure investments, India is poised to absorb 15–25% of the global supply chain shifts in select sectors over the next 3–5 years.
The Road Ahead
India will not replace China’s scale overnight. But in carefully chosen sectors, it has a real opportunity to become a reliable, competitive alternate hub for global supply chains.
For companies seeking resilient, cost-effective, and scalable supply options in a volatile global landscape — the window of opportunity is now.
The winners will be those who act decisively and forge the right partnerships early.
Strategic Priorities for Global Leaders
To navigate this transition effectively, supply chain, procurement, and operations executives should focus on:
- Mapping tariff-exposed supply chains and cost structures
- Diversifying sourcing bases across India, Vietnam, Mexico, and beyond
- Leveraging digital supply chain tools for visibility and risk management
- Aligning with policy incentives to optimise costs and mitigate risk
- Building strategic partnerships with emerging suppliers in India
- Upskilling teams for Industry 4.0 and next-gen manufacturing
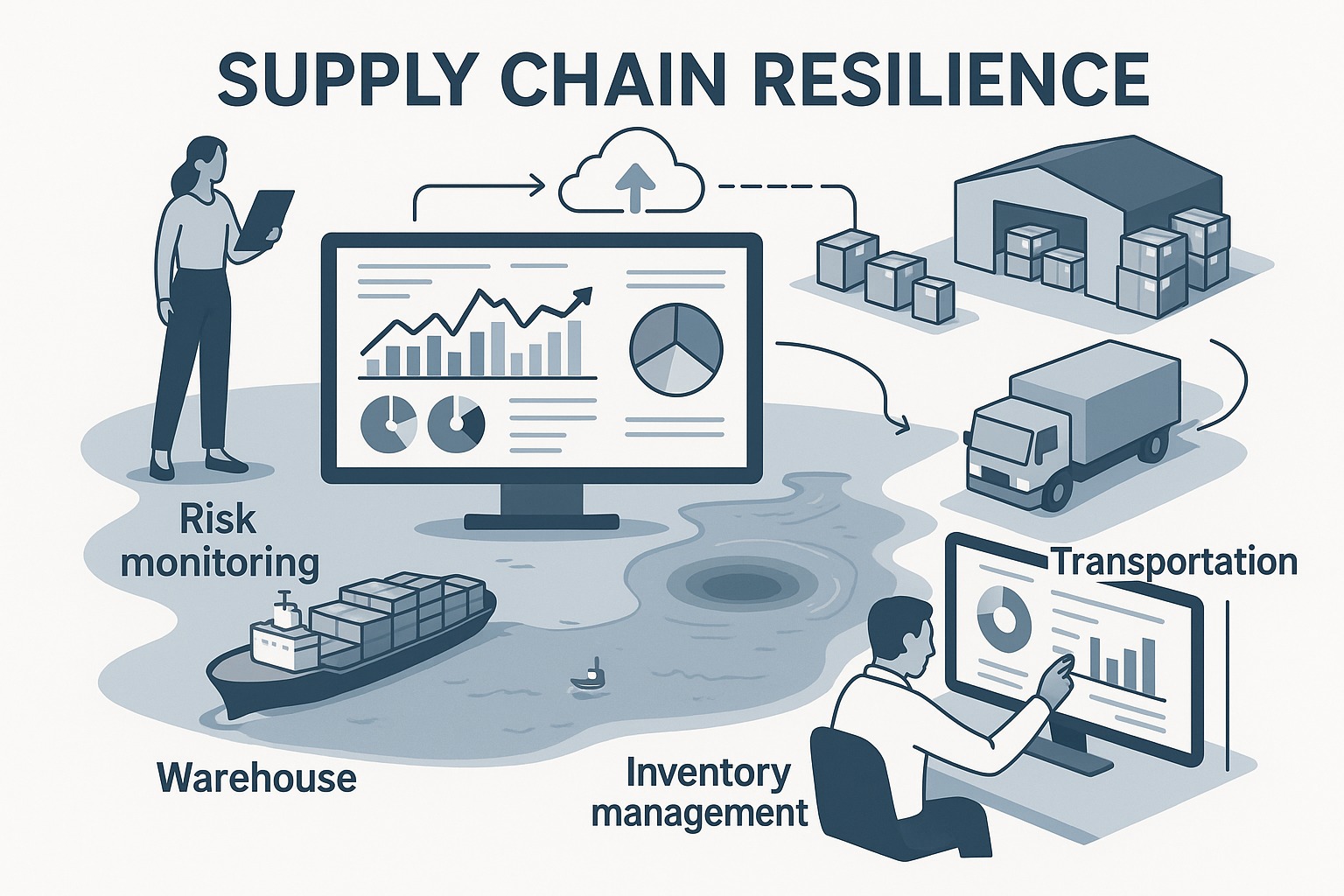
Strategic Training Priorities - Highlight the Empowerment Aspect:
Investing in the skills and knowledge of your supply chain teams is no longer a luxury – it's a cornerstone of building resilience. The outlined training themes are indeed critical and directly empower professionals to navigate today's risks:
Training Area | Why Critical Now? |
---|---|
Smart Manufacturing & Industry 4.0 (Digital Twins, IoT, AI, Cybersecurity) | Mitigate risk of supply shortages via predictive maintenance, simulation, faster design iteration |
Lean, Six Sigma & Operational Excellence | Eliminate waste, boost agility, lower cost buffer against tariff hikes |
Supply Chain Resilience & Risk Management (Vendor mapping, CPFR, risk assessment) | Handle supplier switches, multi-sourcing, improve visibility of tariff-exposed suppliers |
Digital Tools & Analytics | Faster decision-making in uncertain markets; monitor KPIs like lead time, landed costs, OEE |
Workforce Upskilling (Automation, EV) | Offset labor shortages + prepare for tech-enabled shopfloors (especially for EV shift) |
Soft Skills (Change Mgmt., Leadership) | Prepare leaders to navigate ambiguity, communicate strategy shifts fast |
Conclusion - Reinforce the Positive Call to Action:
The 2025 supply chain playbook demands a fundamental shift in mindset – moving beyond simply managing disruption to proactively designing and embedding resilience. For CXOs, CPOs, and senior supply chain professionals in the automotive and automation sectors, this is not just a challenge, but a significant opportunity. By actively mapping tariff exposures, strategically rethinking sourcing geographies, and deeply integrating digital visibility into operations, you can transform potential threats into competitive advantages. Investing in a future-ready workforce, equipped to thrive in tech-enabled, multi-local networks while navigating evolving compliance and sustainability mandates, is equally critical.
The emergence of India, Vietnam, Mexico, and US-allied trade corridors presents a pivotal moment – but the window for decisive action is narrow. Proactive leaders who strategically balance cost, resilience, and policy alignment will not only weather the current storm but will also shape the competitive landscape of tomorrow.
Are your supply chains truly wired for this next decade of complexity? I'm eager to exchange ideas and discuss how we can collectively build more resilient and future-proof supply chains. Let's connect and navigate this new era together!
Sources - Insights synthesized from McKinsey, World Economic Forum, Gartner SCM Outlook 2025, and recent industry discussions in APAC automotive/automation forums @ Supply chain Connect news, Knowledge of Wharton, ET & TOI,